The new granulation line from Romaco Innojet will make its public debut at the upcoming CIPM in Wuhan, China. Romaco will also be showing the latest model in the Kilian K series as well as other tableting technologies.
Romaco Innojet IGL 100 granulation line
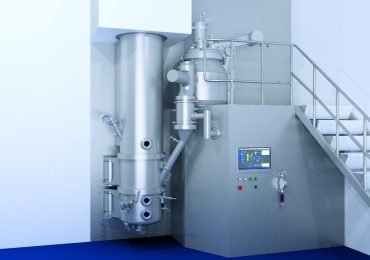
The M 100 high-shear mixer for manufacturing wet granules was developed by Romaco Innojet especially for the new IGL 100 granulation line. In combination with the VENTILUS® V 100 LE dryer, this technology is ideal for achieving compact granules, which are mainly processed during the production of pharmaceutical solids. Numerous different formulations for this conventional granulation process are approved worldwide, which is why Romaco has expanded its product portfolio accordingly. In addition to various fluidised bed systems, Innojet now also offers an end-to-end line concept for manufacturing and subsequently drying wet granules. The first version of the Innojet IGL 100 is designed to handle batches of up to 100 litres. In the medium term, the new IGL series will be capable of processing batches as large as 800 litres.
The line concept ships with central process control and can be cleaned using an integrated WIP (wash in place) system. The transfer from the mixer to the dryer is gravimetric. On the one hand, this design saves space because the machines are installed very close together. On the other, the very short transfer section manages without an external air supply and meets the high requirements for the containment. The wet granules are then dried extremely gently and uniformly in the VENTILUS® V 100 LE. The process air for this purpose is introduced by means of the ORBITER booster. Thanks to Romaco Innojet’s patented air flow bed technology, the movement of the product can be precisely controlled, so that the drying process is not only gentle but also very efficient.
Romaco Kilian K 720 double-sided rotary press
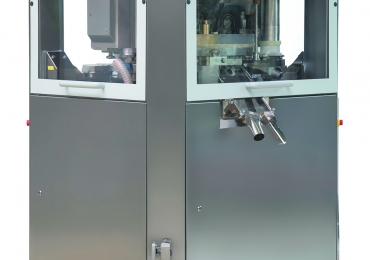
The tablet presses in the Romaco Kilian K series are specially tailored to the needs of the Asian market and impress with their excellent value for money. The K 720 double-sided rotary press was configured by Romaco Kilian for the production of mono and bi-layer tablets and can be switched flexibly between the two operating modes. This high speed press has a maximum output of 1,000,000 tablets per hour. The technology is used both in the pharmaceutical industry and in the non-pharmaceutical sector, and is particularly suited for compressing effervescent tablets, nutraceuticals and drugstore items. The systematic reduction of product loss was a top priority when Romaco Kilian developed the K series. Amongst other features, this is achieved by means of product scrapers, which are in constant contact with the die table surface due to magnetic force.
Targeted measures to improve the Kilian K 720’s productivity, availability and quality have simultaneously increased its overall equipment effectiveness. External fill shoe gears enable a lower process temperature, which is an advantage with temperature sensitive products. Patented bellows result in higher product quality by preventing so-called black spots on the tablets. Punch brake magnets, likewise patented, ensure constant braking forces and a small standard deviation of the tablet weight. The hermetic separation of the tablet press process area from the changeover and service areas moreover restricts cleaning to a minimum and extends the production time of the Romaco Kilian K 720 rotary press.
Romaco Kilian KTP 590X single-sided rotary press
Another exhibit from Romaco Kilian will be the KTP 590X, a model in the successful KTP-X series. The KTP 590X is an extremely versatile single-sided rotary press which can be used to manufacture both mono-layer and bi-layer tablet formats. It can be switched between mono-layer and bi-layer mode without any modifications to the compression roller set-up. Bi-layer tablets can be compressed at any time on the version with three compression rollers. The tablet press is equipped for this purpose with two standard fill shoe modules, which distribute the powder uniformly in the die. Thanks to the optimised paddle design, even poorly flowing or sticky powders can be processed efficiently and compressed homogeneously. With its three separate compression stations, the Kilian KTP 590X is equally suited for manufacturing effervescent tablets. The powder is tamped initially to prevent the formation of air pockets and capping. Then it is pre-compressed and finally converted into finished tablets in the main compression unit. The dwell time is significantly longer owing to the use of Kilian 28/41 tooling, meaning harder tablets can be made, even at high operating speeds. All in all, the Romaco Kilian KTP 590X single-sided rotary press boasts a maximum output of up to 510,000 tablets per hour, even in bi-layer mode. Low process temperatures, efficient cleaning and changeover and a mature hygiene concept – the KTP 590X single-sided rotary press, too, conforms to the design principles of Romaco Kilian’s successful KTP series: “Cool, Fast & Clean”.
On show at CIPM – China International Pharmaceutical Machinery – in Wuhan (China) from November 5 to 7, 2018 (Wuhan International Exposition Center (WIEC), International Hall, Booth A1-14).
Romaco Group
Romaco is a leading international supplier of processing and packaging equipment specialising in engineering technologies for pharmaceutical solids. The group provides individual machines and turnkey solutions for manufacturing and packing powders, granulates, pellets, tablets, capsules, syringes and medical devices. Romaco also serves the food and chemical industries.
The Romaco Group has its headquarters in Karlsruhe (Germany) and is part of the Truking Group, a globally operating high-tech enterprise based in Changsha (China). Truking’s core competency is handling and filling pharmaceutical liquids.
Romaco operates from four European business sites, with a broad portfolio comprised of six established product brands. Noack and Siebler (Karlsruhe, Germany) supply blister, heat-sealing and rigid tube filling machines. Macofar (Bologna, Italy) markets technologies for filling sterile and non-sterile powders and liquids. Promatic (also Bologna, Italy) specializes in cartoners, track & trace systems and case packers. Kilian (Cologne, Germany) offers compression solutions for tableting while Innojet (Steinen, Germany) is an innovation leader for granulation and coating.
More than 600 highly skilled and committed Romaco employees are dedicated to the development of future product technologies and to the continuous implementation of internal improvement processes. Romaco’s multi-brand system solutions are sold worldwide through six Sales & Service Centres and a dense network of local agent organisations. Over 12,000 installations delivered by Romaco are currently in use in more than 180 different countries.