Manufacturers of bulk flow food products can now benefit from optimised detection sensitivity and maximised productivity with the X35 Series Bulk Variant x-ray inspection system from Mettler-Toledo Safeline X-ray. Incorporating high-performance technology and software algorithms developed specifically for bulk flow product lines, the X35 Bulk Variant offers precise removal of contaminated product at high throughput rates. The system is ideal for the inspection of dried fruit and nuts, processed meats, cereals, grains, frozen fruit and vegetables, seafood and dried pet food as well as other bulk flow products boosting production line efficiency and ensuring compliance with food safety legislation.
[wp_ad_camp_4]The X35 Bulk Variant is a single vertical x-ray beam system capable of sensitive detection of dense contaminants, including metal and glass shards, calcified bone, mineral stone and high-density plastic and rubber. The system is capable of throughputs up to 14,000kg/hour, depending on product depth and density, ensuring food safety whilst maximising line efficiency. Advanced detector technology also allows for lower power consumption thereby reducing Total Cost of Ownership (TCO) and increasing bottom line savings.
A specially developed six-scoop rejection mechanism enhances precision contaminant removal with minimal rejection of good product, while a troughed conveyor prevents product spilling from the line, reducing product waste. The X35 Bulk Variant is also available with a range of optional rejection devices to suit the individual needs of specific applications, options include air blast reject systems.
Built according to the principles of the European Hygienic Engineering and Design Group (EHEDG), the X35 Bulk Variant features an Ingress Protection (IP) 69 rated stainless steel cabinet, making it capable of withstanding the harshest wash-down regimes. Sloped surfaces and curved edges minimise bacteria traps and allow water to run off, enabling quick and effective cleaning with minimal downtime, further enhancing line productivity.
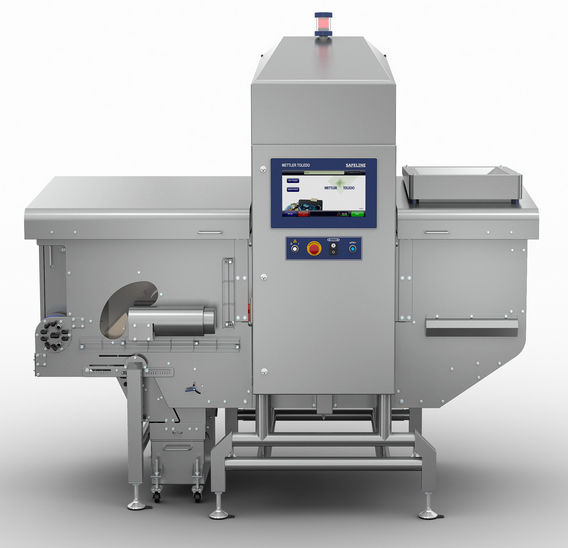
In addition, the x-ray cabinet gives easy access to internal mechanisms for essential maintenance, while the rejection mechanism can be easily removed for cleaning. The conveyor’s automatic tracking feature corrects any belt misalignment without the need to stop the conveyor, maximising production uptime.
The X35 Bulk Variant features a 15.6 inch touchscreen display with intuitive software and automated set-up to facilitate quicker product changeovers. The x-ray system’s PC boasts a large memory to store time-stamped images of every product reject, enhancing traceability for manufacturers to help them demonstrate due diligence in the event of a product recall. The integrated software monitors the system’s Overall Equipment Effectiveness (OEE), providing manufacturers with the relevant information they require to make improvements to machine and line performance, enabling them to further enhance efficiency and productivity. The X35 Bulk Variant can also be connected to the manufacturers’ network, giving authorised personnel the ability to store and analyse inspection and performance data from a remote location.
[wp_ad_camp_2]“With more manufacturers exporting to lucrative European, Australasian and North American markets, they are increasingly finding they have to comply with stringent local food safety legislation, such as the European General Food Law, the Food Standards Australia New Zealand (FSANZ) Act or the US Food Safety Modernisation Act”, explained Paul King, Sales Head at Mettler-Toledo Safeline X-ray. “At the same time, the rising cost of food ingredients, energy and labour, means that manufacturers need to find ways to reduce operating expenses by boosting the efficiency of their lines. With this in mind, our advanced X35 Bulk Variant has been designed to support food processors with precision contaminant detection and removal without compromising on line speeds or production uptime.”